La composition chimique du sable céramique est principalement Al2O3 et SiO2, et la phase minérale du sable céramique est principalement la phase corindon et la phase mullite, ainsi qu'une petite quantité de phase amorphe.Le caractère réfractaire du sable céramique est généralement supérieur à 1800°C, et il s'agit d'un matériau réfractaire aluminium-silicium de haute dureté.
Caractéristiques du sable céramique
● Haute réfractarité ;
● Petit coefficient de dilatation thermique ;
● Conductivité thermique élevée ;
● Forme sphérique approximative, petit facteur d'angle, bonne fluidité et capacité compacte ;
● Surface lisse, pas de fissures, pas de bosses ;
● Matériau neutre, adapté à divers matériaux métalliques de coulée ;
● Les particules ont une résistance élevée et ne se cassent pas facilement.
● La gamme de tailles de particules est large et le mélange peut être personnalisé en fonction des exigences du processus.
Application de sable céramique dans les pièces moulées de moteur
1. Utilisez du sable céramique pour résoudre les veines, le collage du sable, le noyau cassé et la déformation du noyau de sable de la culasse en fonte
● Le bloc-cylindres et la culasse sont les pièces moulées les plus importantes du moteur
● La forme de la cavité interne est complexe et les exigences en matière de précision dimensionnelle et de propreté de la cavité interne sont élevées
● Grand lot

Afin d'assurer l'efficacité de la production et la qualité des produits,
● La production de la chaîne de montage de sable vert (principalement la ligne de coiffage hydrostatique) est généralement utilisée.
● Les noyaux de sable utilisent généralement un processus de boîte froide et de sable enrobé de résine (noyau de coque), et certains noyaux de sable utilisent un processus de boîte chaude.
● En raison de la forme complexe du noyau de sable du bloc-cylindres et du moulage de la tête, certains noyaux de sable ont une petite section transversale, la partie la plus fine de certains blocs-cylindres et noyaux de chemise d'eau de culasse n'est que de 3 à 3,5 mm, et la sortie de sable est étroite, le noyau de sable après la coulée est entouré de fer fondu à haute température pendant une longue période, il est difficile de nettoyer le sable et un équipement de nettoyage spécial est nécessaire, etc. Dans le passé, tout le sable de silice était utilisé dans la coulée production, ce qui a causé des veines et des problèmes d'adhérence du sable dans les pièces moulées de la chemise d'eau du bloc-cylindres et de la culasse.Les problèmes de déformation du noyau et de noyau brisé sont très courants et difficiles à résoudre.
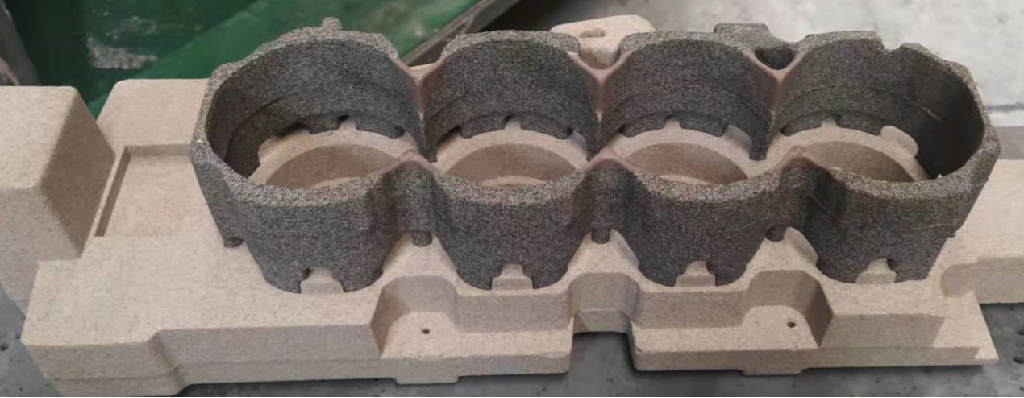
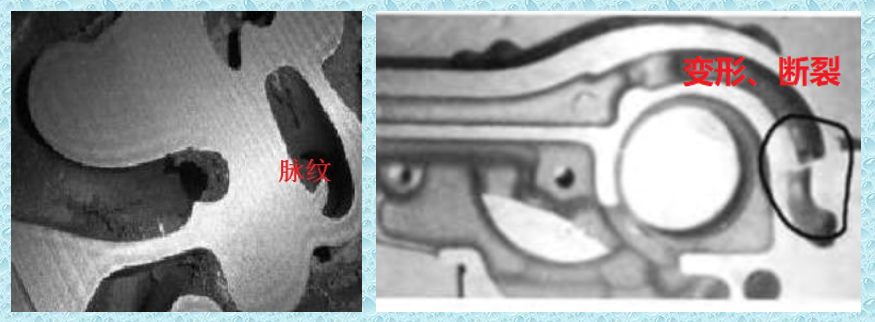
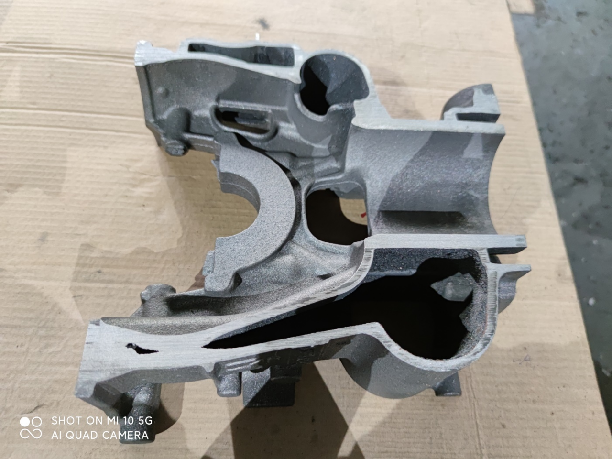
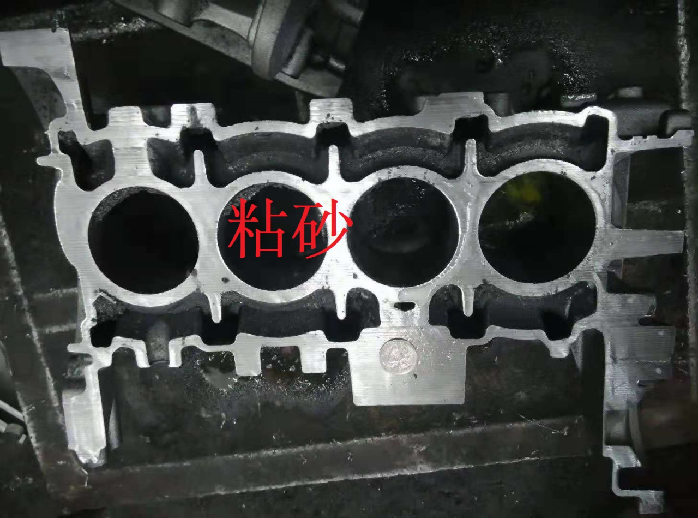
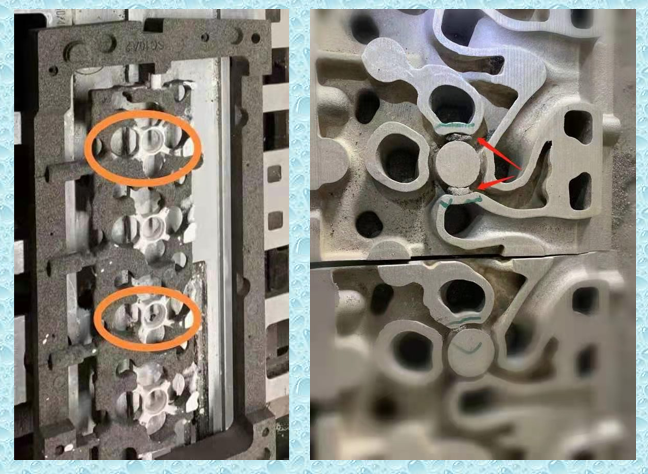
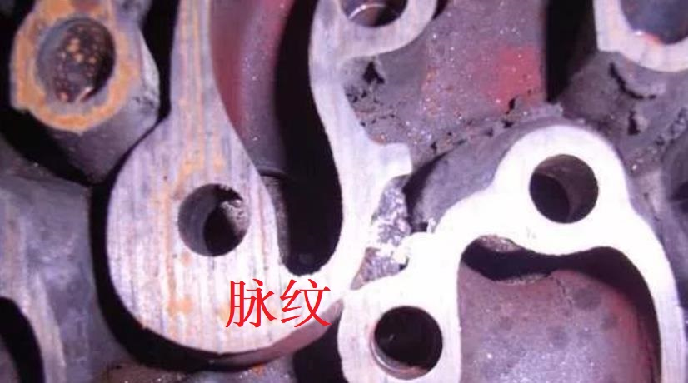
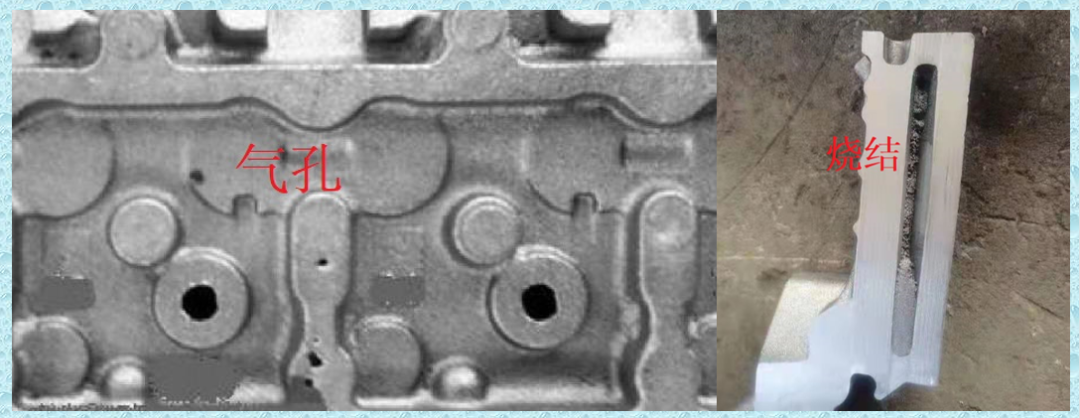
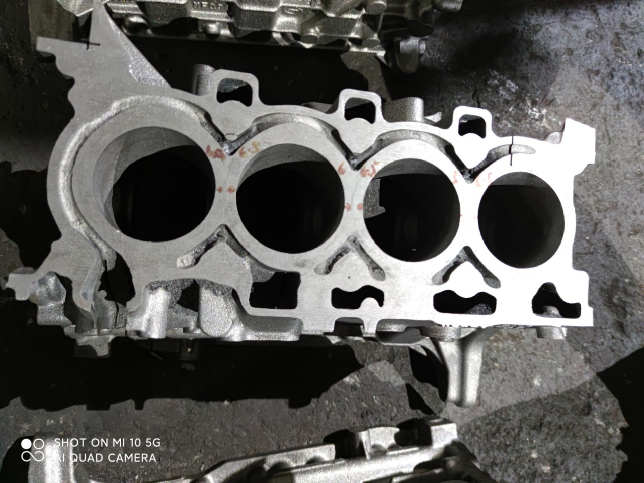
Afin de résoudre ces problèmes, à partir de 2010 environ, certaines sociétés nationales de moulage de moteurs bien connues, telles que FAW, Weichai, Shangchai, Shanxi Xinke, etc., ont commencé à rechercher et à tester l'application de sable céramique pour produire des blocs-cylindres, chemises d'eau de culasse et passages d'huile.Des noyaux de sable égaux éliminent ou réduisent efficacement les défauts tels que le frittage de la cavité interne, le collage du sable, la déformation du noyau de sable et les noyaux cassés.
Les images suivantes sont faites de sable céramique avec un processus de boîte froide.
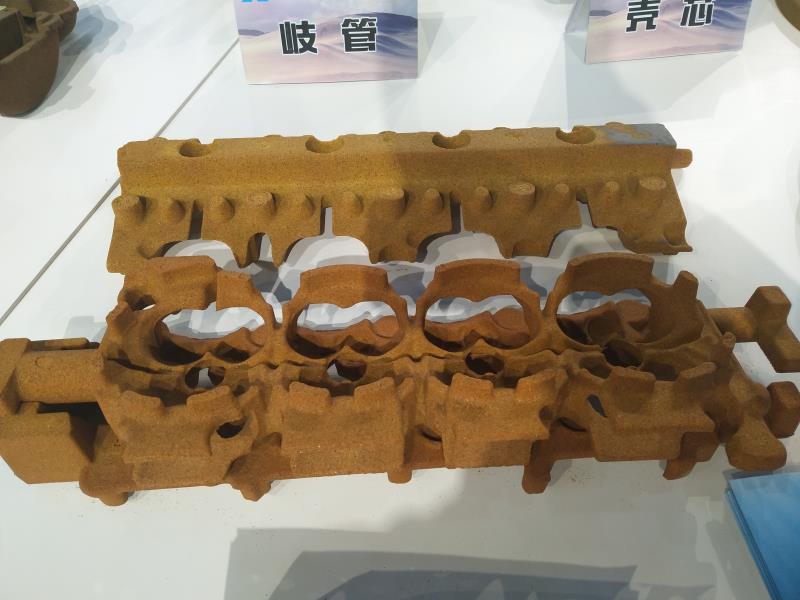
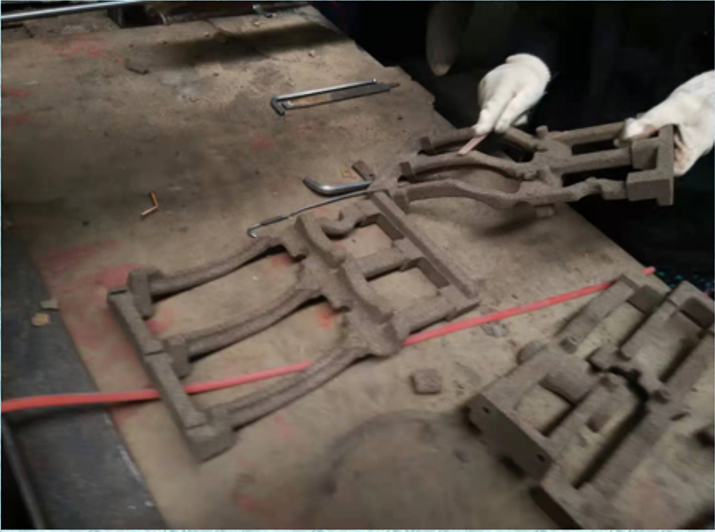
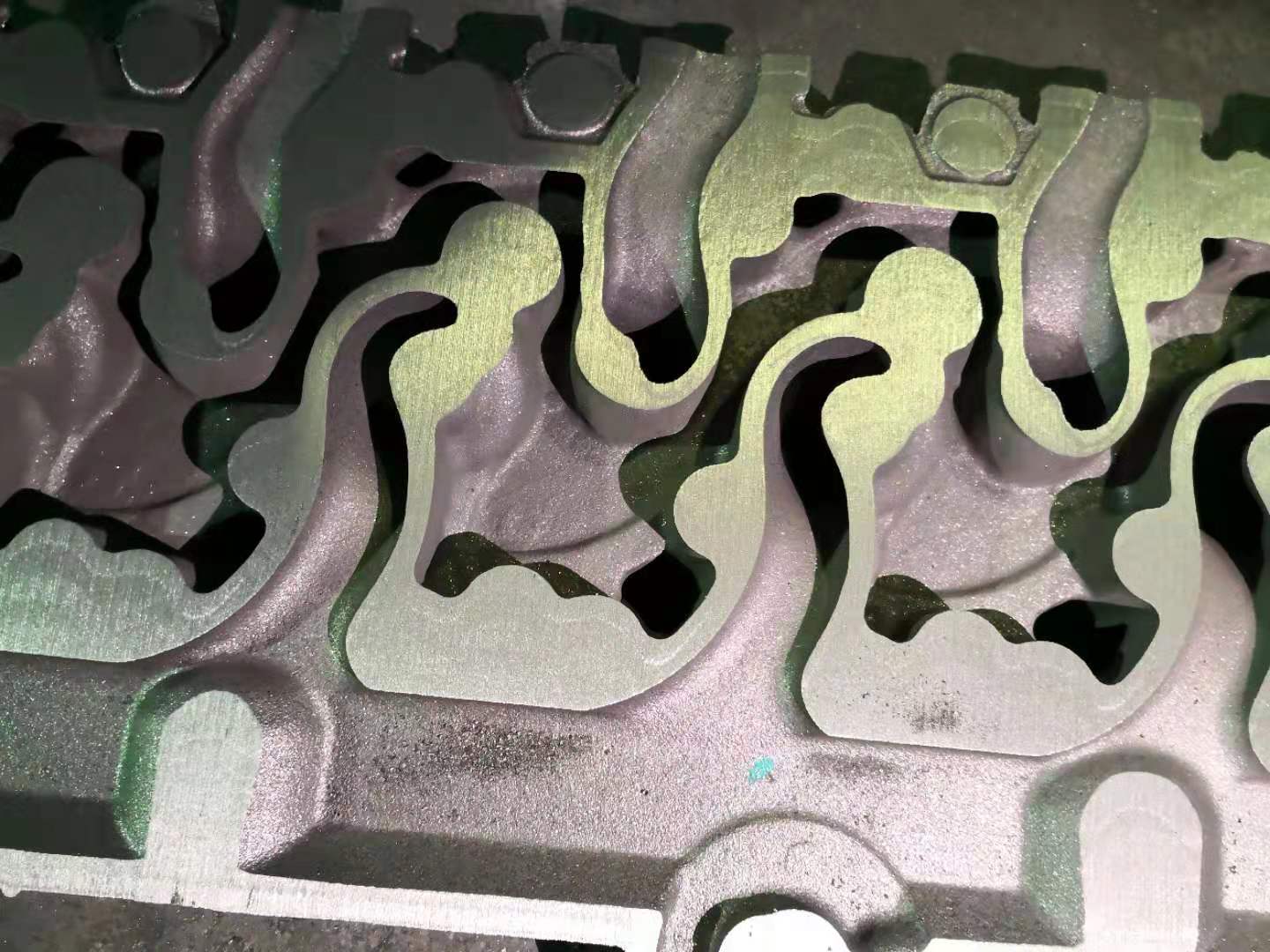
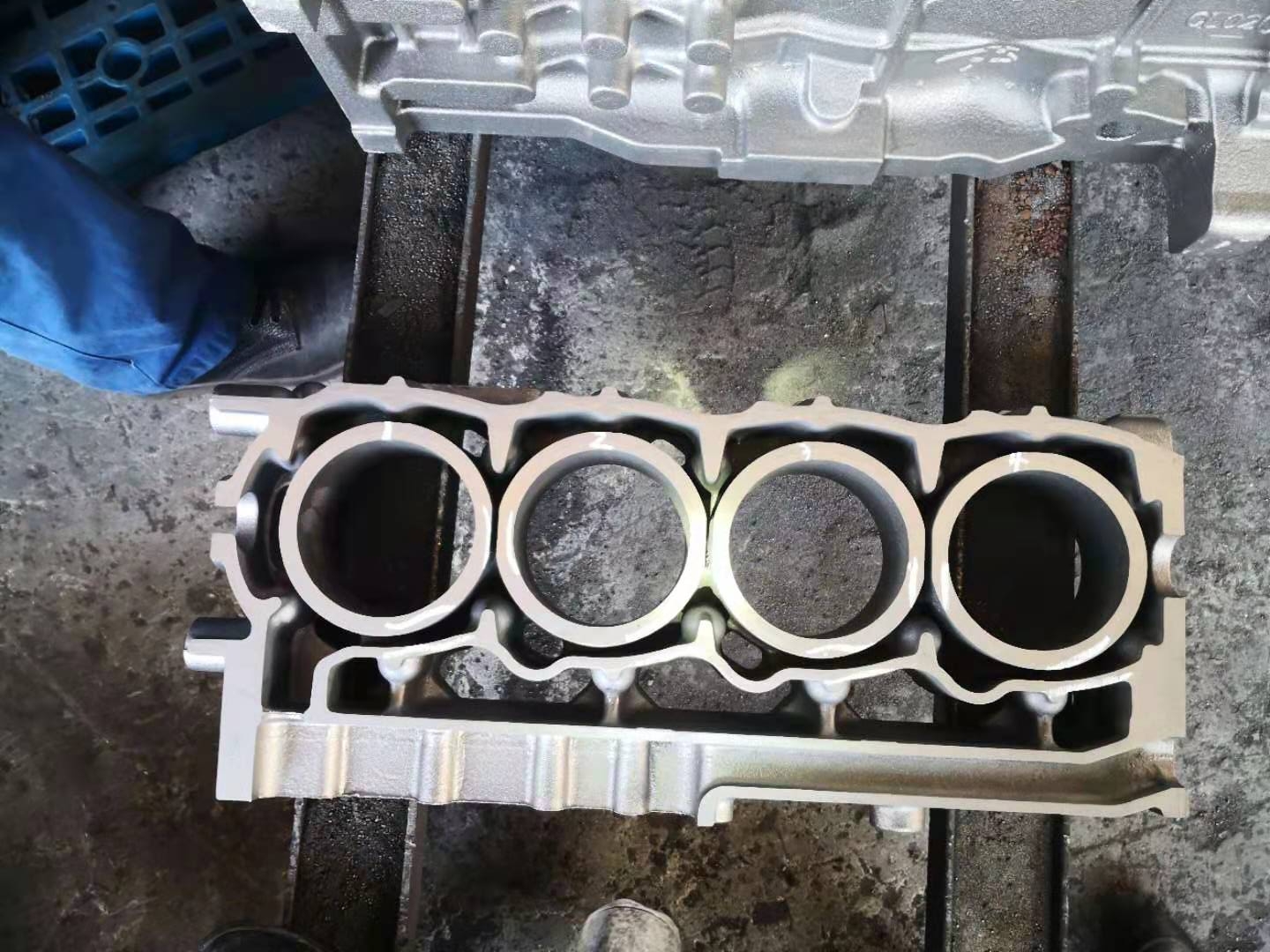
Depuis lors, le sable de récurage mélangé au sable céramique a été progressivement promu dans les processus de boîte froide et de boîte chaude, et appliqué aux noyaux de chemise d'eau de culasse.Il est en production stable depuis plus de 6 ans.L'utilisation actuelle du noyau de sable de la boîte froide est : selon la forme et la taille du noyau de sable, la quantité de sable céramique ajoutée est de 30 % à 50 %, la quantité totale de résine ajoutée est de 1,2 % à 1,8 %, et le la résistance à la traction est de 2,2 à 2,7 MPa.(Données d'essais d'échantillons de laboratoire)
Résumé
Les pièces en fonte du bloc-cylindres et de la culasse contiennent de nombreuses structures de cavité interne étroites et la température de coulée est généralement comprise entre 1440 et 1500 °C.La partie à paroi mince du noyau de sable est facilement frittée sous l'action du fer fondu à haute température, tel que le fer fondu s'infiltrant dans le noyau de sable, ou produit une réaction d'interface pour former du sable collant.Le caractère réfractaire du sable céramique est supérieur à 1800 ° C, tandis que la densité réelle du sable céramique est relativement élevée, l'énergie cinétique des particules de sable de même diamètre et vitesse est 1,28 fois supérieure à celle des particules de sable de silice lors du tir de sable, ce qui peut augmenter la densité des noyaux de sable.
Ces avantages sont les raisons pour lesquelles l'utilisation de sable céramique peut résoudre le problème de l'adhérence du sable dans la cavité interne des pièces moulées de culasse.
La chemise d'eau, les pièces d'admission et d'échappement du bloc-cylindres et de la culasse présentent souvent des défauts veinés.Un grand nombre de recherches et de pratiques de coulée ont montré que la cause première des défauts veineux sur la surface de coulée est l'expansion par changement de phase du sable de silice, qui provoque une contrainte thermique entraînant des fissures à la surface du noyau de sable, ce qui provoque du fer fondu. à pénétrer dans les fissures, la tendance des veines est plus grande surtout dans le procédé de la boîte froide.En fait, le taux de dilatation thermique du sable de silice atteint 1,5 %, tandis que le taux de dilatation thermique du sable céramique n'est que de 0,13 % (chauffé à 1 000 °C pendant 10 minutes).La possibilité de fissuration est très faible à la surface du noyau de sable en raison de la contrainte de dilatation thermique.L'utilisation de sable céramique dans le noyau de sable du bloc-cylindres et de la culasse est actuellement une solution simple et efficace au problème de veinage.
Les noyaux de sable de chemise d'eau de culasse complexes, à parois minces, longues et étroites et les noyaux de sable de canal d'huile de cylindre nécessitent une résistance élevée (y compris une résistance à haute température) et une ténacité, et en même temps doivent contrôler la génération de gaz du sable de noyau.Traditionnellement, le procédé au sable enrobé est majoritairement utilisé.L'utilisation de sable céramique réduit la quantité de résine et permet d'obtenir l'effet d'une résistance élevée et d'une faible génération de gaz.En raison de l'amélioration continue des performances de la résine et du sable brut, le procédé de la boîte froide a de plus en plus remplacé une partie du procédé de sable enrobé ces dernières années, améliorant considérablement l'efficacité de la production et améliorant l'environnement de production.
2. Application de sable céramique pour résoudre le problème de la déformation du noyau de sable du tuyau d'échappement
Les collecteurs d'échappement fonctionnent longtemps dans des conditions d'alternance à haute température, et la résistance à l'oxydation des matériaux à haute température affecte directement la durée de vie des collecteurs d'échappement.Ces dernières années, le pays a continuellement amélioré les normes d'émission des gaz d'échappement des automobiles, et l'application de la technologie catalytique et de la technologie de suralimentation a considérablement augmenté la température de fonctionnement du collecteur d'échappement, atteignant plus de 750 °C.Avec l'amélioration supplémentaire des performances du moteur, la température de travail du collecteur d'échappement augmentera également.Actuellement, l'acier moulé résistant à la chaleur est généralement utilisé, tel que ZG 40Cr22Ni10Si2 (JB/T 13044), etc., avec une température résistante à la chaleur de 950°C-1100°C.
La cavité interne du collecteur d'échappement doit généralement être exempte de fissures, de fermetures à froid, de cavités de retrait, d'inclusions de scories, etc. qui affectent les performances, et la rugosité de la cavité interne ne doit pas être supérieure à Ra25.Dans le même temps, il existe des réglementations strictes et claires sur la déviation de l'épaisseur de la paroi du tuyau.Pendant longtemps, le problème de l'épaisseur de paroi inégale et de la déviation excessive de la paroi du tuyau du collecteur d'échappement a tourmenté de nombreuses fonderies de collecteur d'échappement.

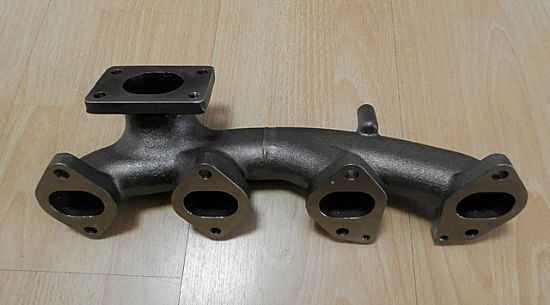
Une fonderie a d'abord utilisé des noyaux de sable recouverts de sable de silice pour produire des collecteurs d'échappement en acier résistant à la chaleur.En raison de la température de coulée élevée (1470-1550°C), les noyaux de sable se déformaient facilement, entraînant des phénomènes hors tolérance dans l'épaisseur de paroi des tuyaux.Bien que le sable de silice ait été traité avec un changement de phase à haute température, en raison de l'influence de divers facteurs, il ne peut toujours pas surmonter la déformation du noyau de sable à haute température, ce qui entraîne une large gamme de fluctuations de l'épaisseur de la paroi du tuyau. , et dans les cas graves, il sera mis au rebut.Afin d'améliorer la résistance du noyau de sable et de contrôler la génération de gaz du noyau de sable, il a été décidé d'utiliser du sable revêtu de sable céramique.Lorsque la quantité de résine ajoutée était de 36% inférieure à celle du sable enduit de sable de silice, sa résistance à la flexion à température ambiante et sa résistance à la flexion thermique ont augmenté de 51%, 67%, et la quantité de génération de gaz est réduite de 20%, ce qui répond à la exigences de processus de haute résistance et faible génération de gaz.
L'usine utilise des noyaux de sable revêtus de sable de silice et des noyaux de sable revêtus de sable céramique pour la coulée simultanée, après avoir nettoyé les pièces moulées, ils effectuent des inspections anatomiques.
Si le noyau est constitué de sable enduit de sable de silice, les pièces moulées ont une épaisseur de paroi inégale et une paroi mince, et l'épaisseur de paroi est de 3,0 à 6,2 mm;lorsque le noyau est constitué de sable revêtu de sable céramique, l'épaisseur de paroi de la pièce moulée est uniforme et l'épaisseur de paroi est de 4,4 à 4,6 mm.comme image suivante
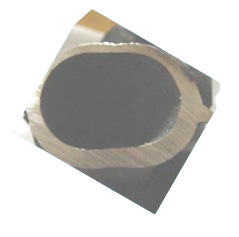
Sable enrobé de sable de silice
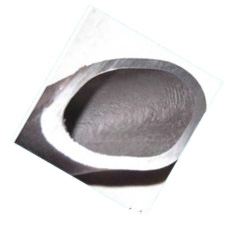
Sable recouvert de sable céramique
Le sable recouvert de sable céramique est utilisé pour fabriquer des noyaux, ce qui élimine la rupture du noyau de sable, réduit la déformation du noyau de sable, améliore considérablement la précision dimensionnelle du canal d'écoulement de la cavité interne du collecteur d'échappement et réduit l'adhérence du sable dans la cavité interne, améliorant la qualité de taux de pièces moulées et de produits finis et réalisé des avantages économiques importants.
3. Application de sable céramique dans le carter du turbocompresseur
La température de fonctionnement à l'extrémité turbine de la coque du turbocompresseur dépasse généralement 600 ° C, et certains atteignent même 950-1050 ° C.Le matériau de la coque doit être résistant aux températures élevées et avoir de bonnes performances de coulée.La structure de la coque est plus compacte, l'épaisseur de la paroi est mince et uniforme et la cavité interne est propre, etc., est extrêmement exigeante.À l'heure actuelle, le carter du turbocompresseur est généralement en fonte d'acier résistant à la chaleur (comme 1.4837 et 1.4849 de la norme allemande DIN EN 10295), et de la fonte ductile résistante à la chaleur est également utilisée (comme la norme allemande GGG SiMo, l'américain fonte nodulaire austénitique à haute teneur en nickel standard D5S, etc.).
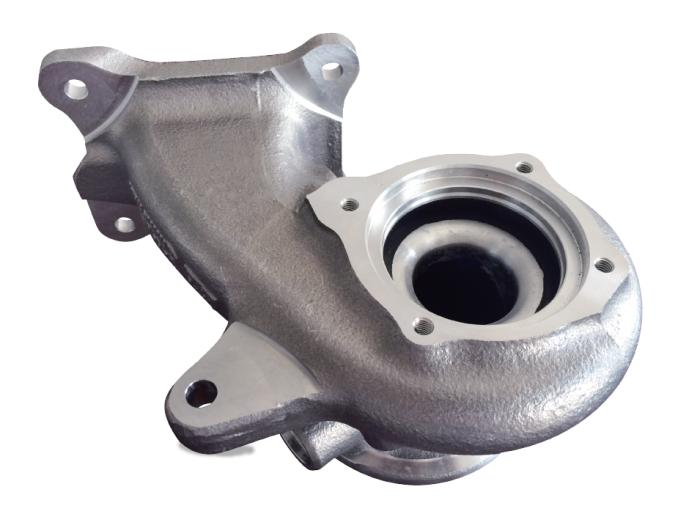
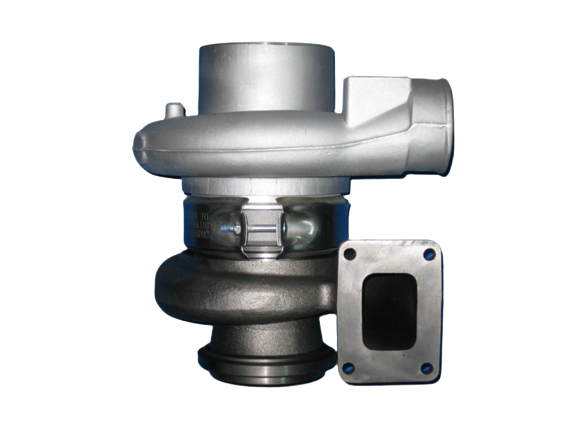
Un carter de turbocompresseur de moteur 1,8 T, matériau : 1.4837, à savoir GX40CrNiSi 25-12, composition chimique principale (%) : C : 0,3-0,5, Si : 1-2,5, Cr : 24-27, Mo : Max 0,5, Ni : 11 -14, température de coulée 1560 ℃.L'alliage a un point de fusion élevé, un taux de retrait élevé, une forte tendance à la fissuration à chaud et une difficulté de coulée élevée.La structure métallographique de la coulée a des exigences strictes sur les carbures résiduels et les inclusions non métalliques, et il existe également des réglementations spécifiques sur les défauts de coulée.Afin d'assurer la qualité et l'efficacité de la production des pièces moulées, le processus de moulage adopte une coulée de noyau avec des noyaux de coquille de sable recouverts d'un film (et certains noyaux de boîte froide et de boîte chaude).Initialement, du sable de récurage AFS50 a été utilisé, puis du sable de silice torréfié, mais des problèmes tels que le collage du sable, des bavures, des fissures thermiques et des pores dans la cavité interne sont apparus à des degrés divers.
Sur la base de recherches et de tests, l'usine a décidé d'utiliser du sable céramique.Initialement acheté du sable revêtu fini (sable 100% céramique), puis acheté des équipements de régénération et de revêtement, et optimisé en continu le processus pendant le processus de production, utilisez du sable céramique et du sable de récurage pour mélanger le sable brut.Actuellement, le sable enrobé est grossièrement mis en œuvre selon le tableau suivant :
Procédé de sable recouvert de sable céramique pour le boîtier du turbocompresseur | ||||
Taille du sable | Taux de sable céramique % | Ajout de résine % | Résistance à la flexion MPa | Débit de gaz ml/g |
AFS50 | 30-50 | 1.6-1.9 | 6.5-8 | ≤12 |
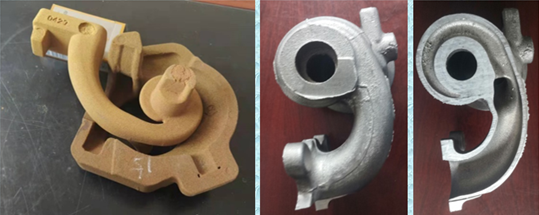
Au cours des dernières années, le processus de production de cette usine a fonctionné de manière stable, la qualité des pièces moulées est bonne et les avantages économiques et environnementaux sont remarquables.Le résumé est le suivant :
un.L'utilisation de sable céramique ou d'un mélange de sable céramique et de sable siliceux pour fabriquer des noyaux élimine les défauts tels que l'adhérence du sable, le frittage, le veinage et la fissuration thermique des pièces moulées, et réalise une production stable et efficace ;
b.Coulée de noyau, efficacité de production élevée, faible rapport sable-fer (généralement pas plus de 2: 1), moins de consommation de sable brut et des coûts réduits ;
c.Le coulage du noyau est propice au recyclage et à la régénération globaux des déchets de sable, et la récupération thermique est adoptée uniformément pour la régénération.La performance du sable régénéré a atteint le niveau du nouveau sable pour le sable de lavage, ce qui a eu pour effet de réduire le coût d'achat du sable brut et de réduire les rejets de déchets solides ;
d.Il est nécessaire de vérifier fréquemment la teneur en sable céramique dans le sable régénéré pour déterminer la quantité de nouveau sable céramique ajouté ;
e.Le sable céramique a une forme ronde, une bonne fluidité et une grande spécificité.Lorsqu'il est mélangé avec du sable de silice, il est facile de provoquer une ségrégation.Si nécessaire, le processus de prise de vue sur sable doit être ajusté.
F.Lorsque vous recouvrez le film, essayez d'utiliser une résine phénolique de haute qualité et utilisez divers additifs avec prudence.
4. Application de sable céramique dans la culasse en alliage d'aluminium du moteur
Afin d'améliorer la puissance des automobiles, de réduire la consommation de carburant, de réduire la pollution par les gaz d'échappement et de protéger l'environnement, les automobiles légères sont la tendance de développement de l'industrie automobile.À l'heure actuelle, les pièces moulées de moteurs automobiles (y compris les moteurs diesel), telles que les blocs-cylindres et les culasses, sont généralement coulées avec des alliages d'aluminium, et le processus de coulée des blocs-cylindres et des culasses, lors de l'utilisation de noyaux de sable, de moulage par gravité de moule métallique et de basse pression casting (LPDC) sont les plus représentatifs.
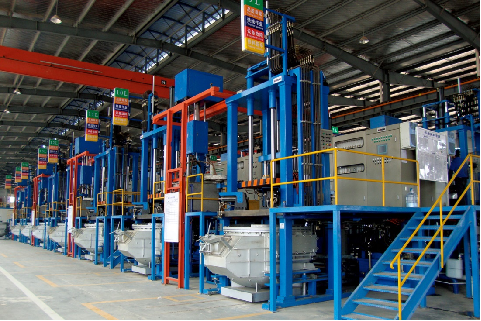
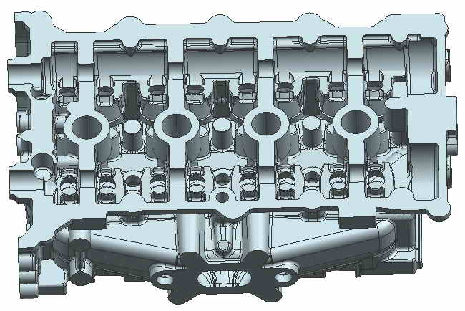
Le noyau de sable, le sable enrobé et le processus de boîte froide du bloc-cylindres et des pièces moulées en alliage d'aluminium sont plus courants, adaptés aux caractéristiques de production de haute précision et à grande échelle.La méthode d'utilisation du sable céramique est similaire à la production de culasse en fonte.En raison de la faible température de coulée et de la faible densité de l'alliage d'aluminium, on utilise généralement du sable à noyau à faible résistance, tel qu'un noyau de sable à boîte froide dans une usine, la quantité de résine ajoutée est de 0,5 à 0,6% et la résistance à la traction est 0,8-1,2 MPa.Le sable de noyau est exigé A la bonne collapsibilité.L'utilisation de sable céramique réduit la quantité de résine ajoutée et améliore considérablement l'affaissement du noyau de sable.
Ces dernières années, afin d'améliorer l'environnement de production et d'améliorer la qualité des pièces moulées, il y a de plus en plus de recherches et d'applications de liants inorganiques (y compris le verre soluble modifié, les liants phosphatés, etc.).L'image ci-dessous est le site de coulée d'une usine utilisant une culasse en alliage d'aluminium de noyau de liant inorganique de sable céramique.
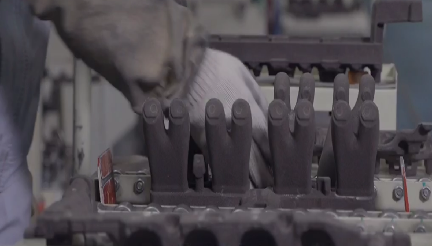
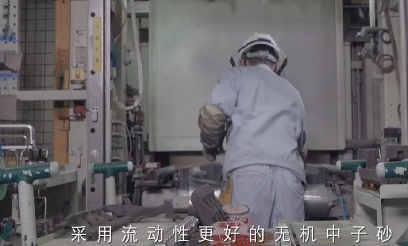
L'usine utilise un liant inorganique de sable céramique pour fabriquer le noyau, et la quantité de liant ajoutée est de 1,8 à 2,2 %.En raison de la bonne fluidité du sable céramique, le noyau de sable est dense, la surface est complète et lisse, et en même temps, la quantité de génération de gaz est faible, cela améliore considérablement le rendement des pièces moulées, améliore l'écrasement du noyau de sable , améliore l'environnement de production et devient un modèle de production verte.
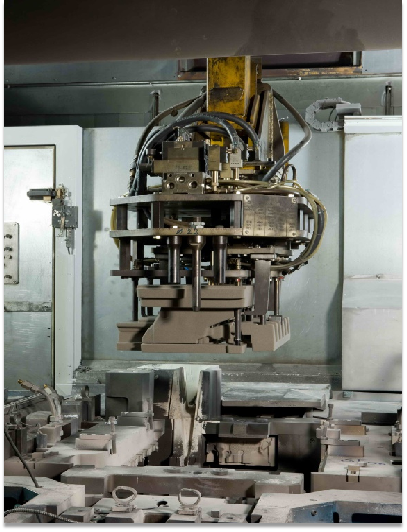
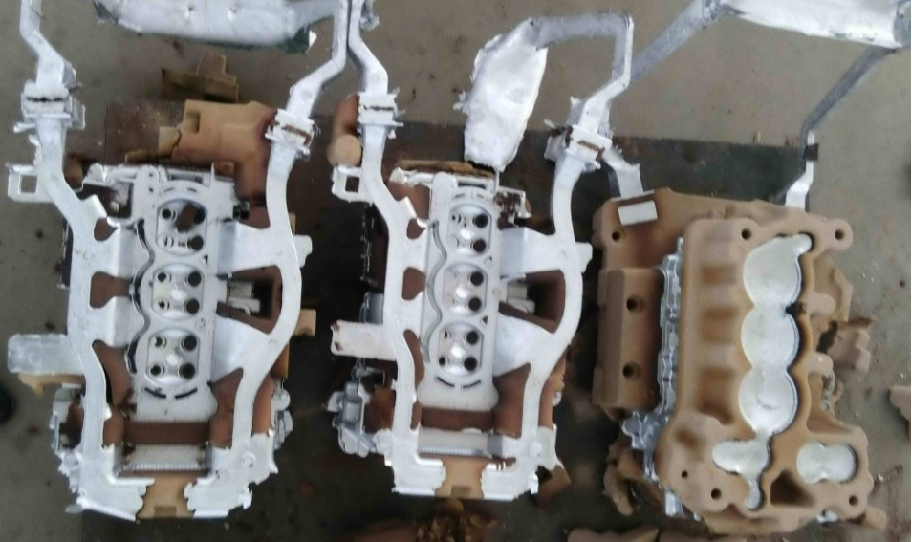
L'application de sable céramique dans l'industrie de la coulée de moteurs a amélioré l'efficacité de la production, amélioré l'environnement de travail, résolu les défauts de coulée et obtenu des avantages économiques significatifs et de bons avantages environnementaux.
L'industrie de la fonderie de moteurs devrait continuer à augmenter la régénération du sable de noyau, améliorer encore l'efficacité d'utilisation du sable céramique et réduire les émissions de déchets solides.
Du point de vue de l'effet d'utilisation et de la portée d'utilisation, le sable céramique est actuellement le sable spécial de coulée avec les meilleures performances globales et la plus grande consommation dans l'industrie de la fonderie de moteurs.
Heure de publication : 27 mars 2023