In sand casting, more than 95% use silica sand. The biggest advantage of silica sand is that it is cheap and easy to get. However, the disadvantages of silica sand are also obvious, such as poor thermal stability, the first phase transition occurs at about 570°C, high thermal expansion rate, easy to break, and the dust generated by the break is very harmful to human health. At the same time, with the rapid development of the economy, silica sand is widely used in the construction industry, glass industry, ceramics and other industries. There is a lack of high-quality and stable silica sand. Finding its substitutes is an urgent problem for the whole world.
Today let’s talk about the difference of some the common raw sands in foundry business, according sndfoundry team many years experiences, also welcome more friends to join talk.
1.Common Raw Sands in Foundry
1.1 Natural sand
Natural sand, which is from the nature, such as silica sand, chromite sand, zircon sand, magnesium olive sand etc.
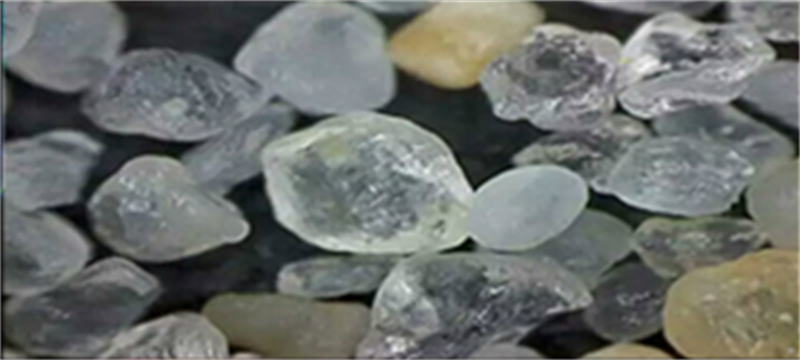
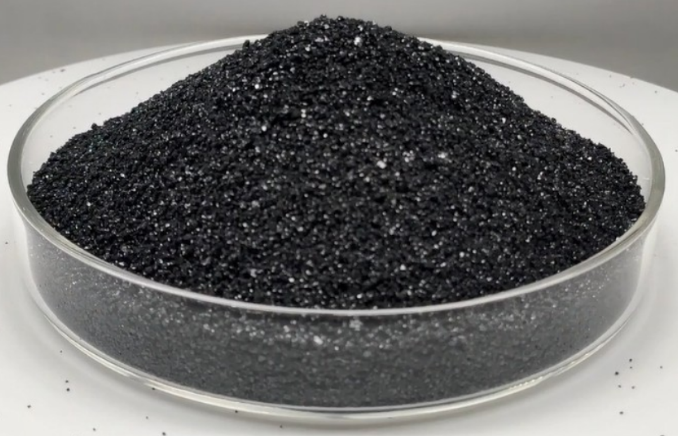
1.2 Artificial sand
Such as Artificial silica sand, aluminum silicate series artificial spherical sand, etc.
Here we mainly introduce the aluminum silicate series artificial spherical sand.
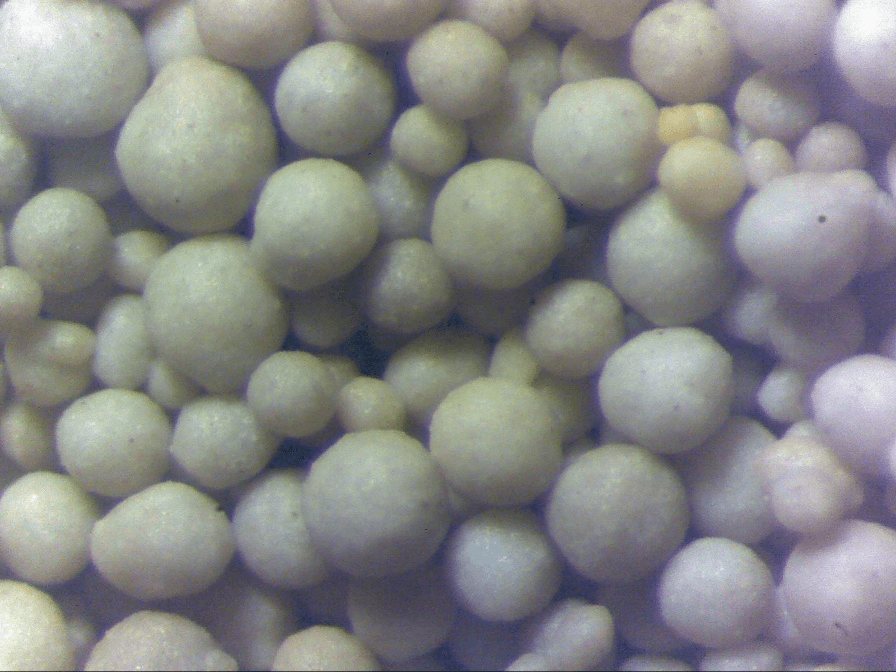
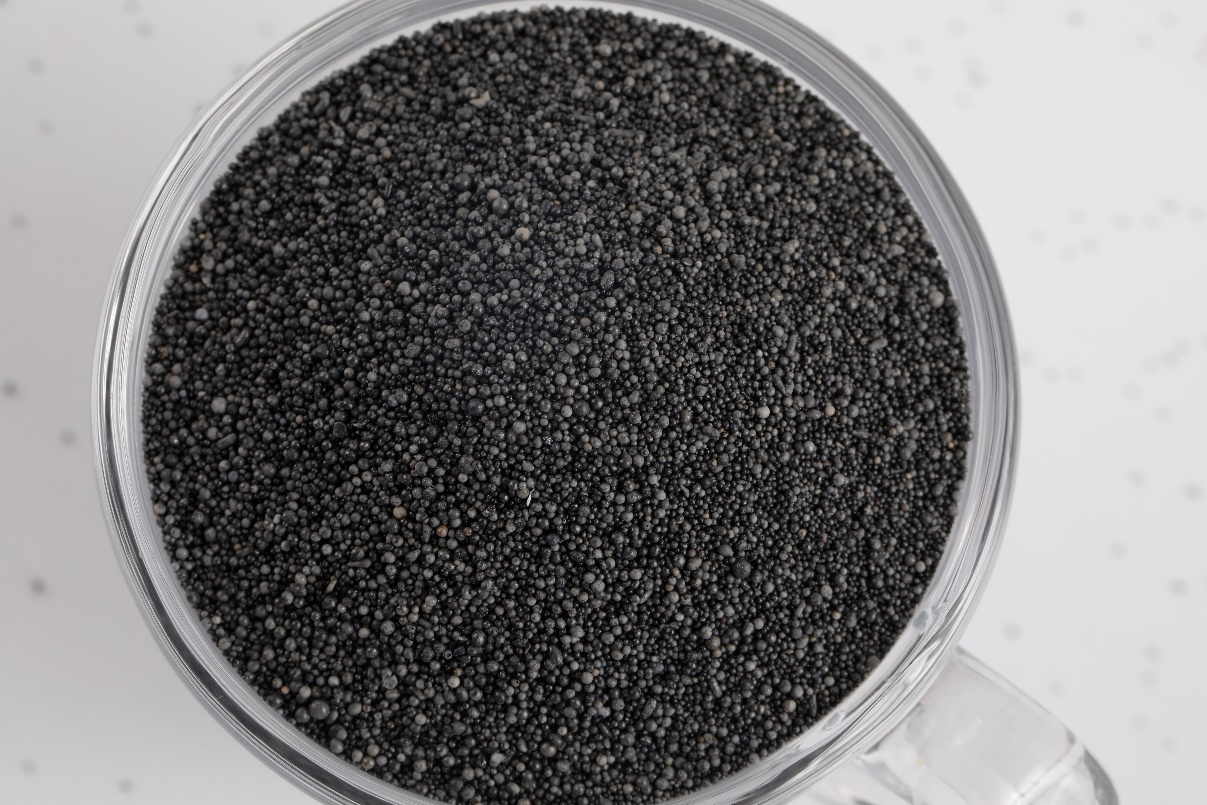
2. Aluminum silicate series artificial spherical sand
Aluminum silicate series artificial spherical sand, also known as "ceramic foundry sand", “Cerabeads”, “ceramic beads”, "ceramsite", “Synthetic spherical sand for casting (Moon sand)”, "mullite beads", "high refractoriness spherical sand", "Ceramcast", "Super sand", etc., there is no uniformity names in the world and standards are also varied. (We call ceramic sand in this article)
But there are three same points to identify them as follow:
A. Using aluminum silicate refractory materials (bauxite, kaolin, burnt gems, etc.) as raw materials,
B. The sand particles are spherical after melting or sintering;
C. The mainly chemical composition including Al2O3, Si2O, Fe2O3, TiO2 and other oxide.
Due to there are many manufactures in China of ceramic sand, there are various colors and surface from different processes and different original place of raw material, and different Al2O3 content and the produce temperature.
3. The parameters of sand for foundry
Sands | NRD/℃ | T.E.(20-1000℃)/% | B.D./(g/cm3) | E. | T.C.
(W/m.k) |
pH |
FCS | ≥1800 | 0.13 | 1.8-2.1 | ≤1.1 | 0.5-0.6 | 7.6 |
SCS | ≥1780 | 0.15 | 1.4-1.7 | ≤1.1 | 0.56 | 6-8 |
Zircon | ≥1825 | 0.18 | 2.99 | ≤1.3 | 0.8-0.9 | 7.2 |
Chromite | ≥1900 | 0.3-0.4 | 2.88 | ≥1.3 | 0.65 | 7.8 |
Olive | 1840 | 0.3-0.5 | 1.68 | ≥1.3 | 0.48 | 9.3 |
Silica | 1730 | 1.5 | 1.58 | ≥1.5 | 0.49 | 8.2 |
Note: Different factory and place sands, the data will have some difference.
Here is just the common data.
3.1 Chilling characteristics
According to the chilling capacity formula, the chilling capacity of sand is mainly related to three factors: thermal conductivity, specific heat capacity, and true density. Unfortunately, these three factors are different for sand from different manufacturers or origins, so in the development During the application process of wear-resistant steel castings, we found that chromite sand has the best chilling effect, fast cooling speed, and high wear-resistant hardness, followed by fused ceramic sand, silica sand, and sintered ceramic sand. , the wear-resistant hardness of the casting will be lower by 2-4 points.
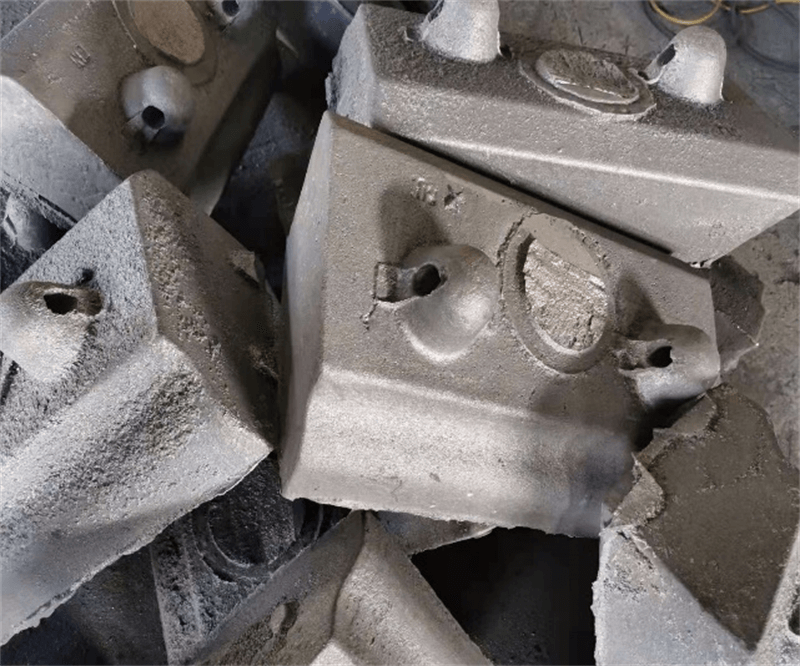
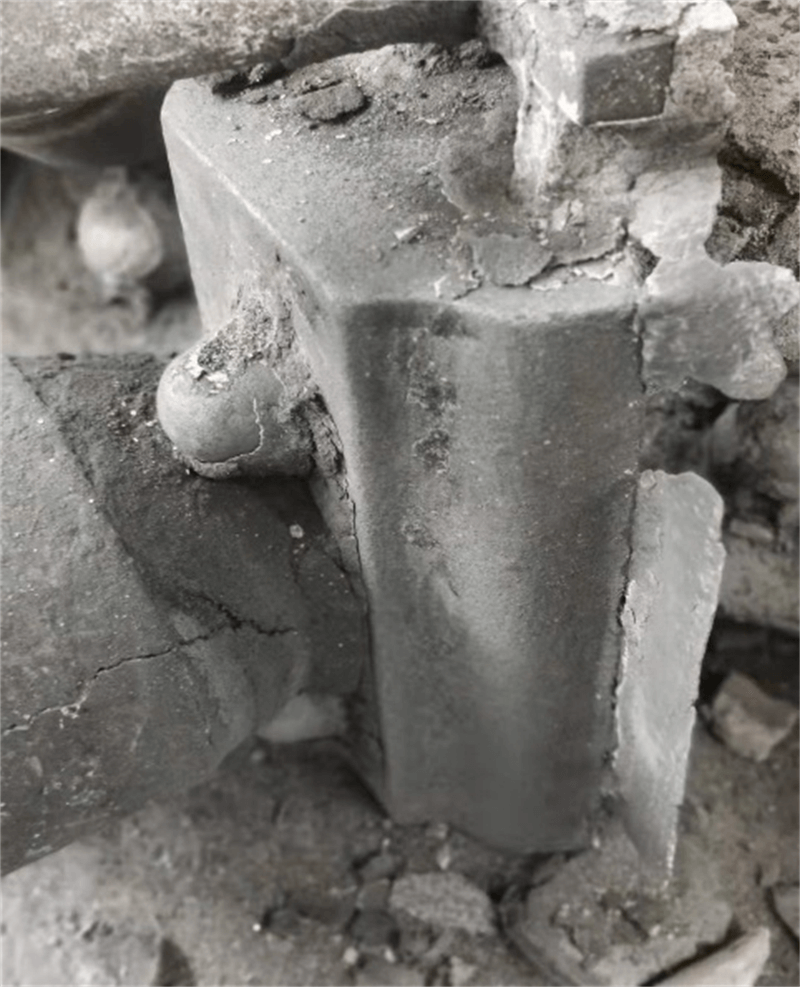
3.2 Collapsibility compare
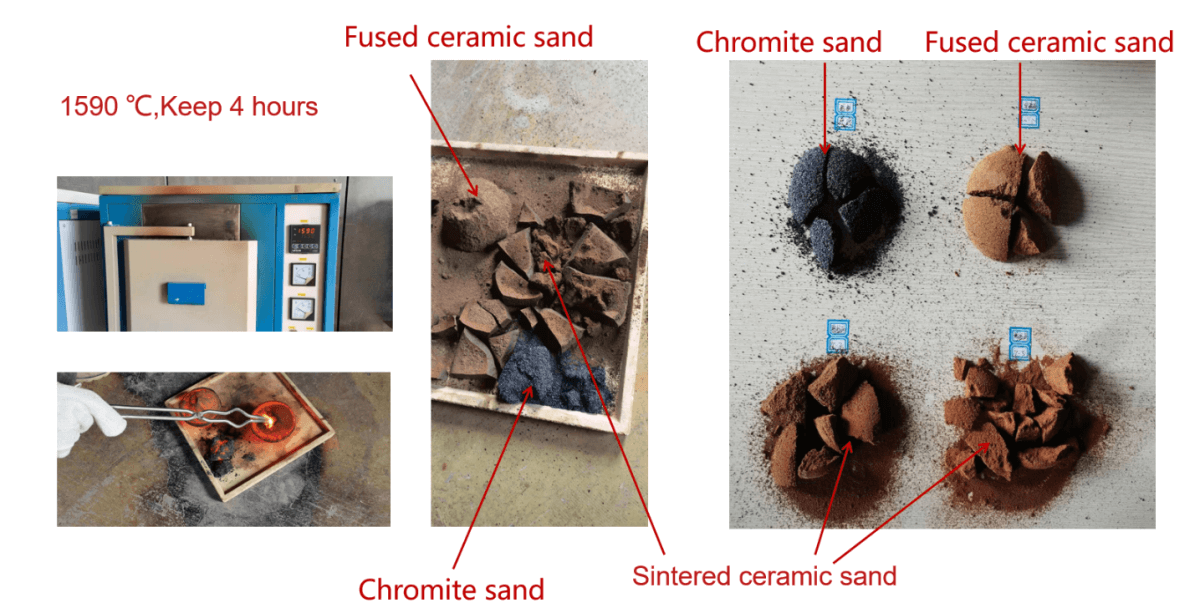
As above picture, three kinds of sands keep 4 hours with 1590 ℃ in the furnace.
The sintered ceramic sand collapsibility is the best one. This property also have successfully applicated in Aluminum casting produce.
3.3 The strength compare of sands mold for foundry
A The parameters of resin coated sand mold for foundry
Sands | H.T.S.(MPa) | R.T.S.(MPa) | A.P.(Pa) | L.E. Rate (%) |
CS70 | 2.1 | 7.3 | 140 | 0.08 |
CS60 | 1.8 | 6.2 | 140 | 0.10 |
CS50 | 1.9 | 6.4 | 140 | 0.09 |
CS40 | 1.8 | 5.9 | 140 | 0.12 |
RSS | 2.0 | 4.8 | 120 | 1.09 |
Note:
1. The resin type and amount are the same, the original sand is AFS65 size, and the same coating conditions.
2. CS: Ceramic sand
RSS: Roasted Silica sand
H.T.S.: Hot tensile strength.
R.T.S.: Room tensile strength
A.P.:Air permeability
L.E. Rate: Liner expansion rate.
3.4 Excellent reclamation rate of ceramic sand
Thermal and machine reclamation method are both good suitable ceramic sand, due to its’ particle’s high strength, high hardness, high wear resistance, ceramic sand almost is the highest regeneration times raw sand in sand foundry business. According our domestic customers reclamation data, ceramic sand can reclaimed at least 50 times. Here are some cases share:
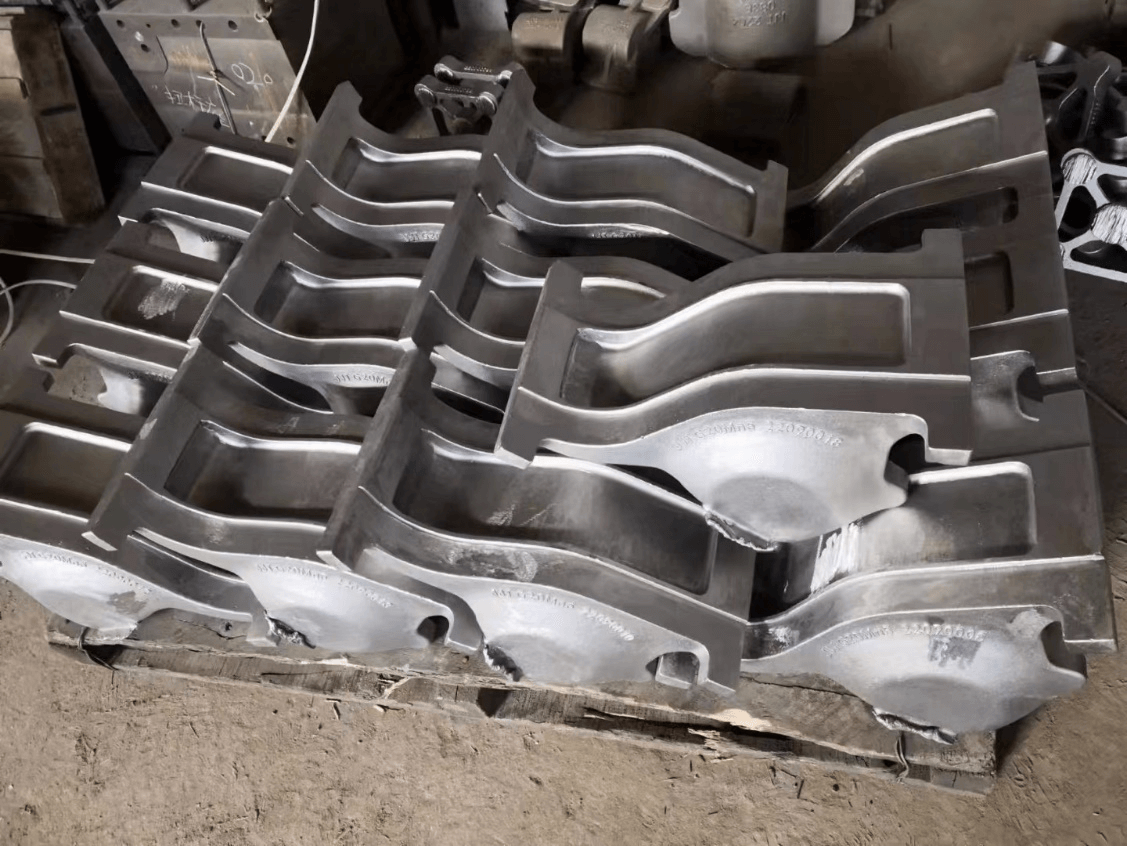
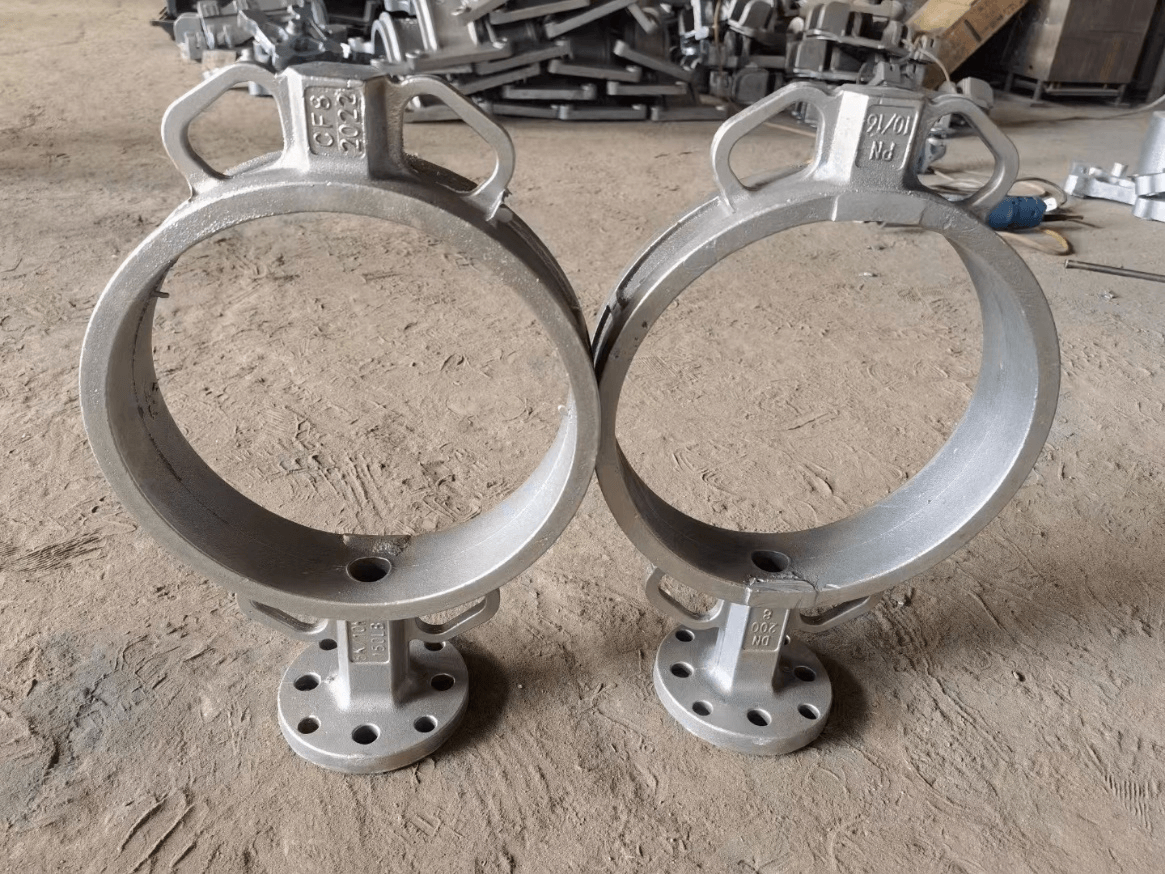
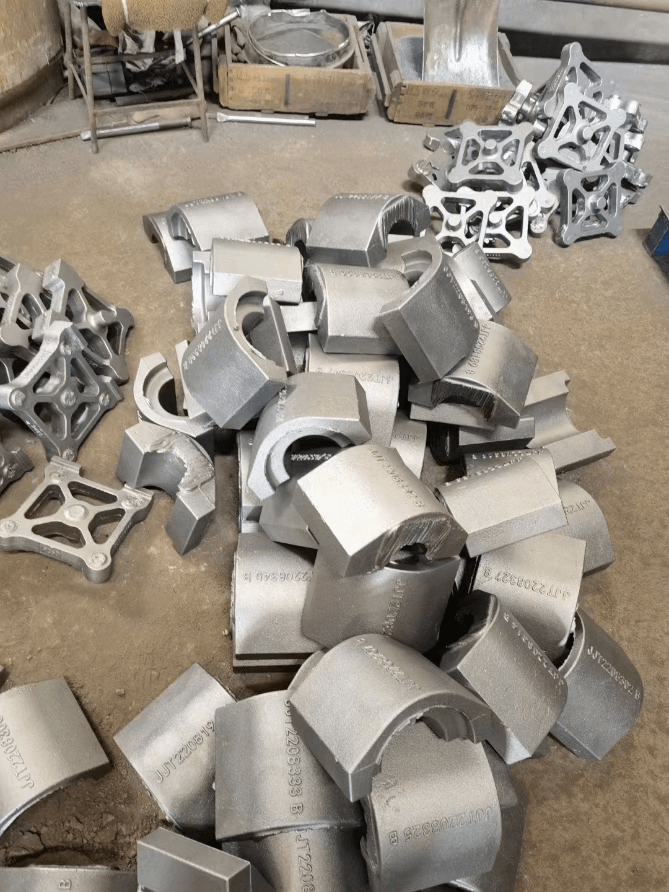
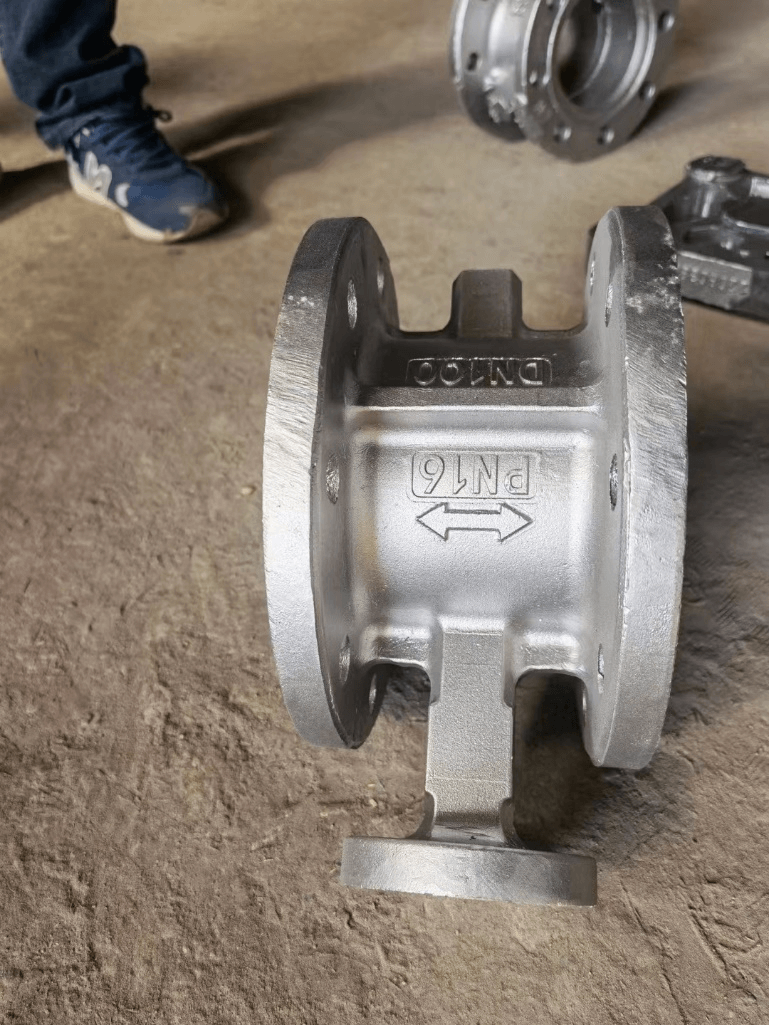
In recently ten years, due to ceramic sand high refractoriness, ball shape which could help reduce resin addition around 30-50%, uniform component composition and stable grain size distribution, good air permeability, little thermal expansion and higher renewable recycling characteristics etc., as a a neutral material, it has widely applicable to multiple castings including cast iron, cast steel, cast aluminum, cast copper, and stainless steel. Application foundry processes have Resin coated sand, Cold box sand, 3D printing sand process, No-bake resin sand, Investment process, Lost foam process, Water glass process etc.
Post time: Jun-15-2023